AI for the Quantification of Mineral Phases in Mineral Residues Using SEM and XRD (KIMmich)
Summary
In the KIMmich project, artificial intelligence ( AI) is used for the automated determination of the mineralogical composition of industrial residues such as ashes and slags. By combining high-resolution SEM analyses with XRD measurements, a robust training dataset is created, enabling the development of AI models for reliable identification and quantification of mineral phases. The goal is to facilitate the use of these materials as secondary raw materials and to enable the targeted control of processes such as waste incineration or metallurgy within an ecologically optimized material cycle.
The project is funded by the AI Production Network Augsburg.
Problem Statement
Mineral residues such as ashes and slags are generated in large quantities during industrial processes - particularly in thermal waste treatment and metallurgy. Managing these residues presents a major ecological and economic challenge: these materials hold significant potential as secondary raw materials - for example, as fillers in the construction industry or as aggregates in concrete. However, recycling requires compliance with construction and environmental quality standards, which is both time-consuming and labor-intensive. The mineralogical composition of these materials is a key factor influencing their suitability for construction and environmental applications, and it can already be influenced during the formation process of the residues. Nevertheless, the quantitative determination of mineral phases is complex and requires expert knowledge. This is where the KIMmich project comes in.
Project Description
The KIMmich project aims to combine analytical techniques with methods of artificial intelligence ( AI) to efficiently and automatically determine the mineralogical composition of industrial residues. Two well-established analytical methods are employed:
- Scanning Electron Microscopy ( SEM) provides highly spatially resolved information on the local chemical composition.
- X-ray Diffraction ( XRD) enables insights into the crystalline phase distribution of the bulk material.
In the initial phase of the project, synthetic mixtures of typical mineral phases are simulated-also using AI methods-in order to generate a comprehensive training dataset. This dataset is supplemented by real measured reference samples to ensure high data diversity and practical relevance. Based on this foundation, AI models are trained and validated in multiple steps. Targeted tests are conducted to evaluate the prediction accuracy for phase quantification.
Subsequently, the trained models are applied to real samples. The evaluation is carried out using two different AI approaches, each employed for the quantification of mineral phases:
- Convolutional Neural Networks ( CNNs), a proven method from image processing, analyze spectral and image-like data based on local patterns and edges.
- Vision Transformer ( ViTs), on the other hand, use so-called self-attention mechanisms to capture complex, global relationships in the data-even across longer spatial distances.
The use of both models enables a systematic comparison in terms of accuracy, robustness, and interpretability, with the goal of identifying the most suitable architecture for reliable phase recognition.
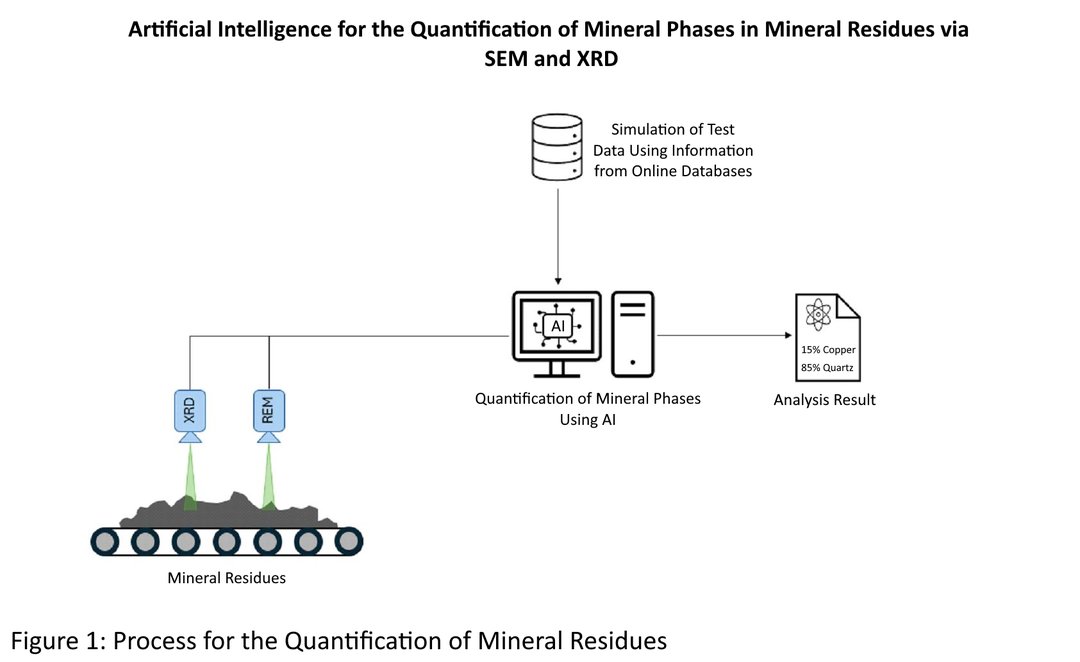
Project Objective
The goal of KIMmich is the automated and reliable identification and quantification of mineral phases in industrial residues using artificial intelligence. The results are intended to support the targeted control of the processes that generate these materials, such as in incineration plants or metallurgical operations. In this way, not only can the main product be optimized, but also the quality and reusability of by-products can be purposefully managed. In the long term, this contributes to the eco-design of mineral residues.
Potential Application Areas
-
Use of mineral residues as industrial aggregates for asphalt and concrete
-
Assessment of the environmental compatibility of ashes and slags
-
Automated material characterization in the laboratory or directly along the process line through integration with sensor data (e.g., LIBS, NIR)
-
Contribution to circular value creation through more targeted utilization of secondary raw materials
Picture of the Team
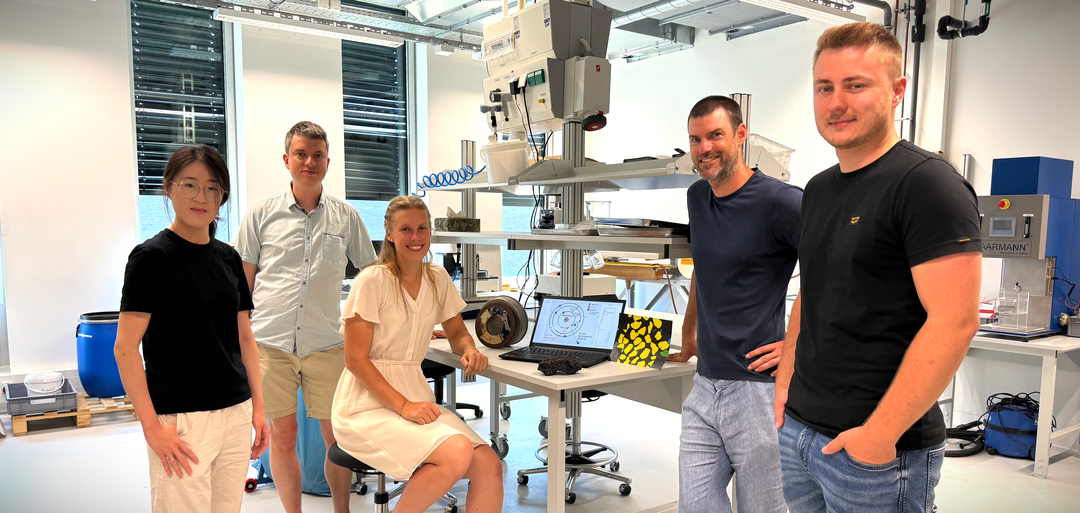